Quality design in printed circuit boards depends on strict adherence to industry standards and manufacturing requirements. Understanding these critical specifications ensures optimal performance, reliability, and compliance throughout the production process. Addressing these essential requirements is fundamental for manufacturers seeking to deliver high-quality electronic products.
Understanding IPC Standards for PCBs
The Institute for Printed Circuits (IPC) has established comprehensive standards that serve as the foundation for quality PCB design and manufacturing worldwide. These standards ensure consistency, reliability, and safety across the electronics industry, providing essential guidelines that manufacturers and designers must follow to deliver high-performance products.
Foundation Standards for Visual Quality and Acceptability
IPC-A-600 stands as the cornerstone standard for printed board acceptability, establishing clear criteria for visual quality assessment. This standard defines acceptable limits for various defects including pits, scratches, inclusions, and other internal imperfections. Manufacturers rely on IPC-A-600 to maintain uniform quality guidelines, ensuring only boards meeting stringent visual standards proceed through production. The standard provides detailed photographic references and measurement criteria that eliminate subjective interpretation during inspection processes.
IPC-A-610 extends quality control to electronic assemblies, covering soldering quality, component placement accuracy, and assembly cleanliness. This standard proves invaluable for original equipment manufacturers (OEMs) who need precise guidelines for catching common issues like component misalignments and inadequate solder joints during the assembly phase.
Performance and Design Specifications
IPC-6012 focuses specifically on qualification and performance specifications for rigid PCBs. This standard establishes requirements for electrical, thermal, and mechanical properties, ensuring boards can reliably handle expected operational stress and environmental conditions. Compliance with IPC-6012 directly correlates with enhanced product durability and extended operational lifespan.
IPC-2221 provides comprehensive design guidelines covering materials selection, layout optimization, and conductor spacing requirements. This standard serves as the primary reference for PCB designers, establishing best practices that reduce manufacturing errors and production challenges. Following IPC-2221 during the design phase significantly improves consistency while maximizing PCB efficiency and overall quality performance.
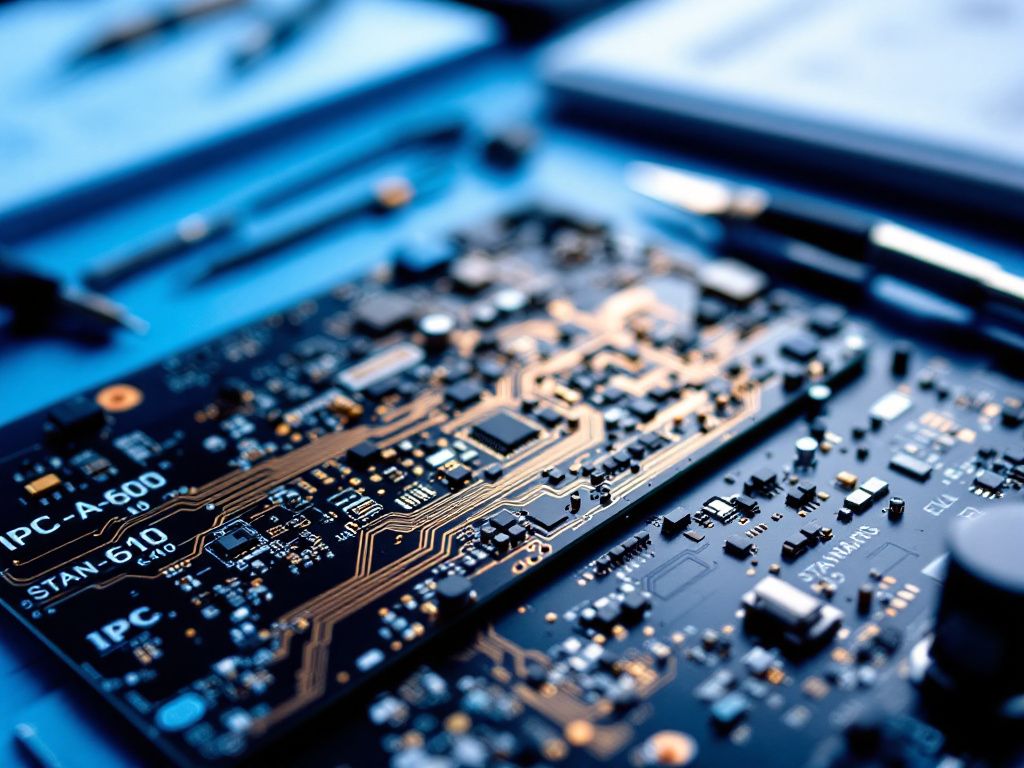
Key Design Considerations for PCB Manufacturers
Successful PCB manufacturing hinges on meticulous attention to critical design considerations that directly impact board performance and long-term reliability. These fundamental aspects must be carefully evaluated during the design phase to ensure optimal manufacturing outcomes and product durability.
Material Selection and Thermal Management
The foundation of quality PCB design begins with selecting appropriate materials that can withstand operational demands. High Tg materials exceeding 170°C are essential for preventing delamination under thermal stress. These materials provide superior thermal stability, ensuring the PCB maintains structural integrity throughout its operational lifecycle. Copper selection plays an equally vital role, with smooth copper profiles minimizing skin effect issues that can compromise signal integrity. The thermal conductivity of base materials should exceed 0.4 W/m.K to facilitate efficient heat dissipation, preventing component failure due to excessive temperatures.
Stack-up Design and Symmetry Requirements
Maintaining symmetry in PCB stack-up design is crucial for preventing warpage and ensuring dimensional stability during manufacturing and operation. Balanced copper distribution across layers minimizes internal stress that could lead to board distortion. The stack-up configuration directly affects impedance control and signal integrity, making careful layer arrangement essential for high-performance applications. Proper dielectric thickness selection between layers ensures consistent electrical characteristics while supporting mechanical stability requirements.
Conductor Spacing and IPC-2221 Compliance
Adherence to IPC-2221 specifications for conductor spacing ensures reliable electrical performance and manufacturing feasibility. Minimum trace width and spacing requirements prevent electrical shorts while maintaining signal integrity. These specifications account for manufacturing tolerances and environmental factors that could affect conductor performance. Proper spacing also facilitates effective heat dissipation and reduces electromagnetic interference between adjacent traces. Following these guidelines enhances overall PCB durability and operational reliability, making IPC-2221 compliance fundamental to quality design practices.
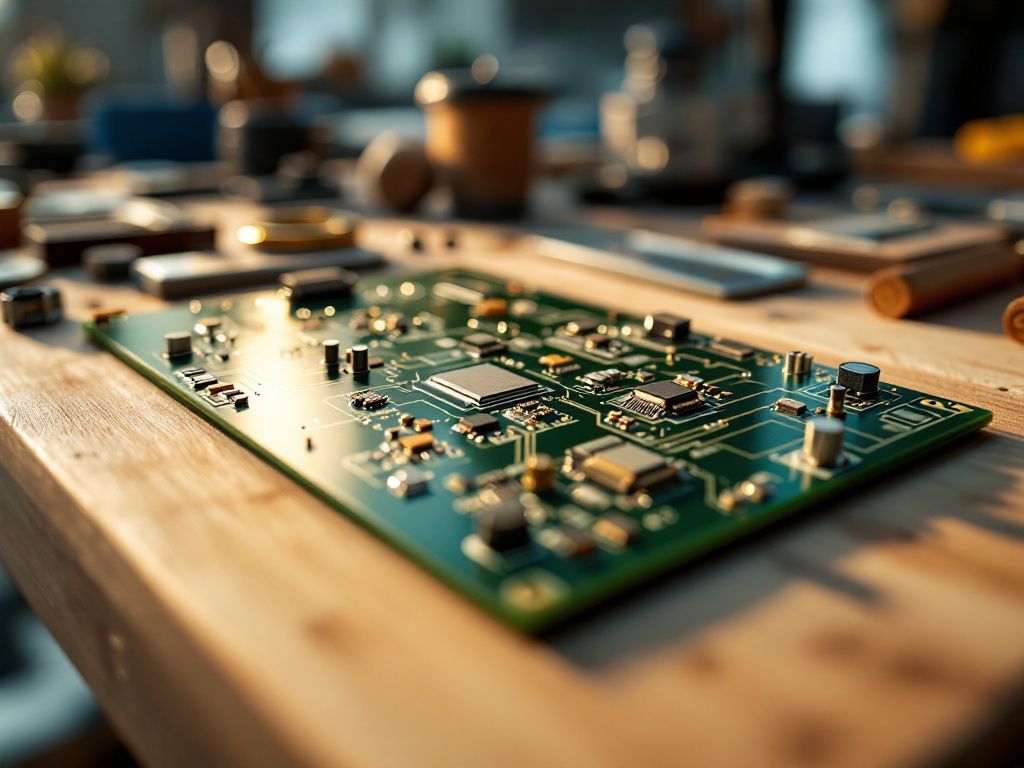
PCB Fabrication Instructions and Data Requirements
Successful PCB manufacturing hinges on comprehensive fabrication instructions and precise data requirements that guide production teams through every critical step. These specifications serve as the blueprint for transforming design concepts into functional circuit boards while maintaining the highest standards of precision and quality.
Essential Gerber and Drill Data Specifications
Gerber data forms the foundation of PCB fabrication, requiring files in RS-274X format with clear layer identification and proper aperture definitions. The drill data must include Excellon format files specifying exact hole sizes, positions, and plating requirements. Manufacturing teams rely on these files to program automated equipment, ensuring each via and component hole meets design specifications within ±0.002 inches tolerance. Comprehensive drill charts accompanying the data prevent misinterpretation and reduce production errors that could compromise board functionality.
Netlist data, while not mandatory, provides crucial verification capabilities by enabling cross-referencing between design intent and manufactured output. This ASCII format file helps identify potential shorts or opens before production begins, significantly reducing revision cycles and associated delays.
Board Outline and Thickness Requirements
Accurate board outline documentation requires 1:1 scale drawings with complete dimensional details and tolerance specifications. Critical measurements include hole-to-edge distances, X-Y coordinates for all features, and routing program requirements for complex board profiles. Finished board thickness specifications must account for copper weight, dielectric materials, and surface finish applications, typically ranging from 0.062 inches for standard designs to specialized thicknesses for high-frequency applications.
Surface Finish and Quality Standards
Surface finish specifications directly impact solderability and long-term reliability. Common options include HASL, ENIG, and OSP, each requiring specific processing parameters and quality checkpoints. These instructions must detail acceptable thickness ranges, coverage requirements, and visual acceptance criteria to ensure consistent manufacturing outcomes and prevent assembly issues downstream.
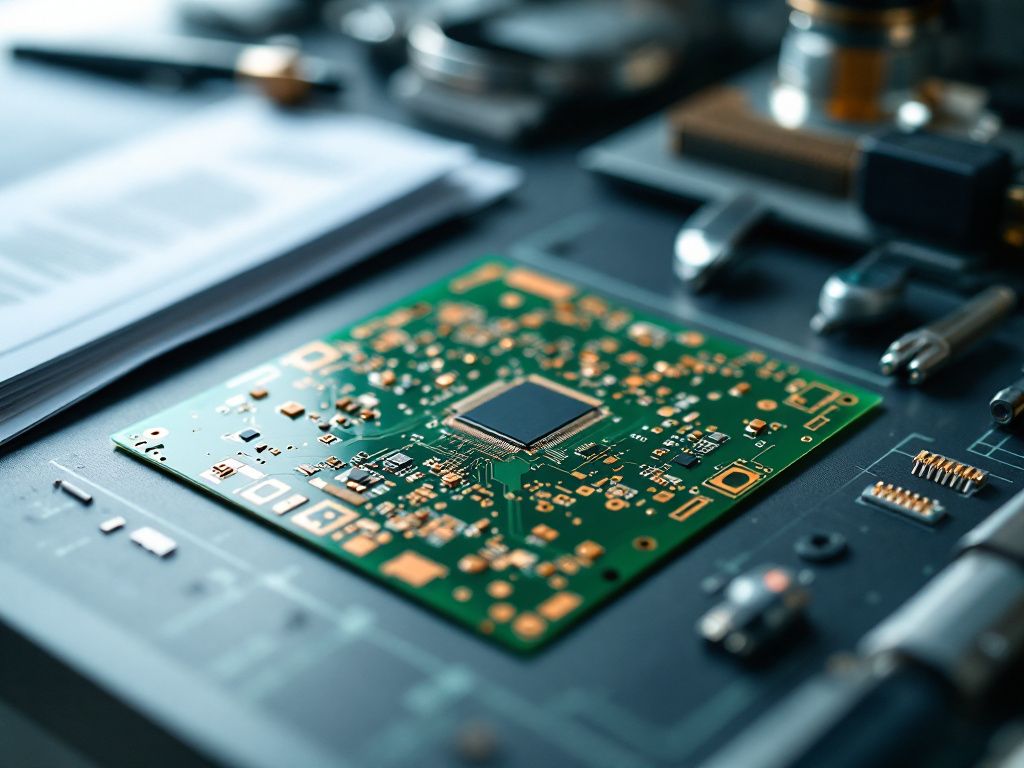
Environmental Concerns and Compliance in PCB Manufacturing
Environmental stewardship in PCB manufacturing has become increasingly critical as regulatory frameworks tighten and industry awareness of ecological impact grows. The Environmental Protection Agency (EPA) has established comprehensive guidelines that manufacturers must navigate to ensure both product quality and environmental responsibility.
TSCA and RCRA Regulatory Framework
The Toxic Substances Control Act (TSCA) serves as the primary regulatory foundation governing PCB-related materials and processes. Under TSCA provisions, manufacturers must carefully manage any equipment or materials containing polychlorinated biphenyls (PCBs), particularly during emergency situations or natural disasters. The Resource Conservation and Recovery Act (RCRA) complements these requirements by establishing specific protocols for hazardous waste management throughout the manufacturing lifecycle.
Current TSCA regulations require manufacturers to implement stringent assessment procedures for damaged PCB-containing electrical equipment. These protocols become particularly crucial when addressing environmental releases during emergency situations, where rapid response and proper containment are essential for compliance.
PCB Remediation Waste Management
Effective management of PCB remediation waste requires adherence to specific EPA guidelines that address contaminated materials and disposal procedures. Manufacturers must establish comprehensive waste storage protocols, implement proper container marking systems, and maintain detailed manifesting and recordkeeping requirements. The EPA’s guidance documents provide clear frameworks for determining appropriate cleanup levels based on waste type and intended site use.
Verification and Documentation Standards
Compliance verification involves establishing deed restrictions where necessary and implementing covering or capping procedures for contaminated areas. Manufacturers must demonstrate adherence to cleanup standards through documented testing and monitoring protocols that meet EPA specifications.
Eco-Friendly Manufacturing Practices
Modern PCB manufacturing increasingly emphasizes sustainable practices that exceed minimum compliance requirements. These eco-friendly approaches include implementing closed-loop water systems, utilizing lead-free soldering processes, and adopting energy-efficient production methods that reduce overall environmental impact while maintaining product quality standards.
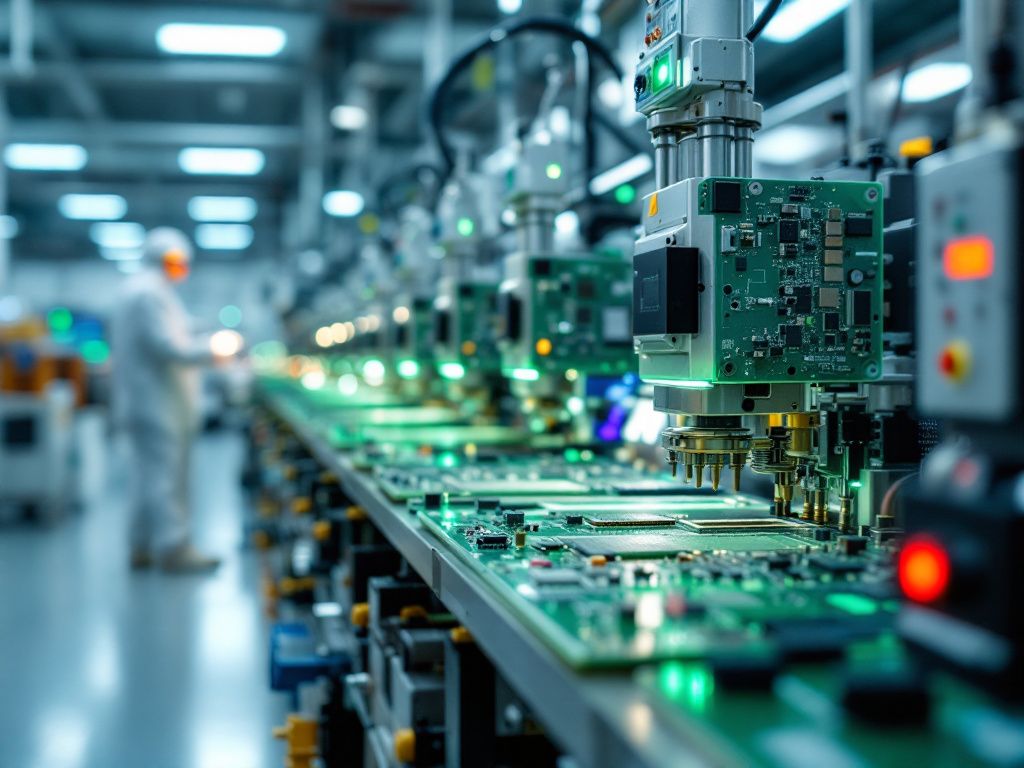
What to remember about PCB requirements
The landscape of PCB requirements continues to evolve with advancing technology and stricter environmental regulations. Future developments will likely emphasize enhanced sustainability practices, tighter precision standards, and increased integration of automated compliance monitoring. Manufacturers who stay ahead of these evolving requirements will maintain competitive advantages while ensuring consistent quality delivery.